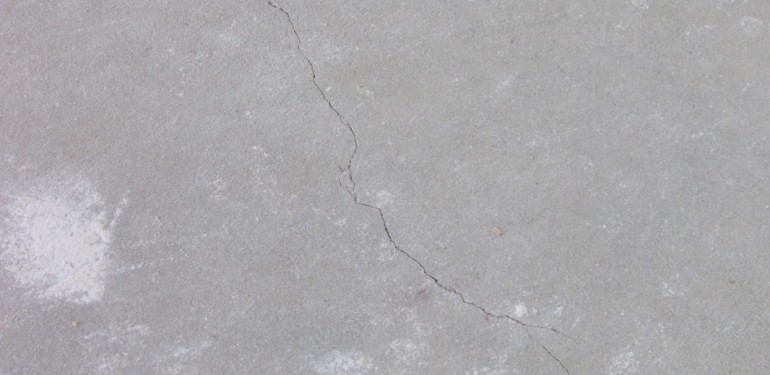
Types of Concrete Cracks – Plastic Shrinkage Cracking
Small or fine cracks identified on a concrete slab are generally deemed acceptable as part of minor settlement, weathering, or poor finishing of its surface. However, a competent building inspector should be able to not only classify the severity of the cracking, but also appropriately investigate the cause of the cracking. The following blog focuses on cracks that form as a result of what is known as plastic shrinkage cracking.
What is plastic shrinkage cracking?
Plastic shrinkage cracks are so-called because they form while the concrete is still plastic, ie has not set. Whilst the member begins to dry it shrinks, and as such cracks may form. These cracks are not always evident immediately after pouring and may be discovered the following day.
Plastic shrinkage cracks may be in a random pattern or may be roughly parallel to each other. Cracks are usually straight, ranging in length from 25mm to 2m but are usually 300 to 600mm long. They rarely appear in areas towards the edge of the slab.
The width of the crack can be up to 3mm wide at the surface and may penetrate right through the concrete member, although generally cracks taper from the surface. Plastic shrinkage cracking should always be monitored as cracks may widen due to subsequent drying shrinkage and thermal movement.
What causes plastic shrinkage cracking?
The general principal around plastic shrinkage cracking is that the rate of evaporation at the surface of the concrete is greater than the amount supplied to it. The concrete surface dries out and shrinks at a time when it is yet to achieve its desired strength, and therefore cracks are evident on the surface. This process can be likened to when cracks appear on the surface of clay soil as it dries.
The rate of evaporation from the surface of a concrete member is dependent upon a number of factors involving both mix design and environmental factors.
How can plastic shrinkage cracking be avoided?
The addition of moisture to the mix may avoid plastic shrinkage cracking, although the extra bleeding characteristics of these mixes may lead to problems such as plastic settlement cracking, and the mix may not comply with the requirements of the slump test.Controlling the rate of drying of the surface of the concrete (evaporation rate) is the key to avoiding plastic shrinkage cracking. The following may be adopted to minimise the incidence of plastic shrinkage cracking:
- Dampen the subgrade and formwork, ensuring that any excess water is removed prior to placing concrete.
- In hot weather, lowering the temperature using chilled mixing water or replacing some of this water with crushed ice.
- Avoid pouring concrete prior to the temperature reaching thirty degrees, and when the forecast temperature exceeds thirty-six degrees, concrete must not be poured.
- Protect the surface from drying out by the use of wind breaks.
- Apply aliphatic alcohols over the surface immediately after screeding and while there is plenty of bleed water on the surface; repeat the application in severe conditions. These products reduce the rate of evaporation from the surface. They are not a substitute for curing.
- Commence curing of concrete promptly after finishing and for the specified period.
- The use of sufficient proportions of synthetic or steel fibres in concrete can provide improved control of plastic cracking.
How is plastic shrinkage cracking assessed when a building inspection is carried out?
All cracking will be monitored by your Perth building inspector throughout the build process. All cracking should be classified in accordance with AS 2870, and advice should be given accordingly.
Generally if plastic shrinkage cracking is less than 1mm in width, it will not require rectification as plastic shrinkage cracking rarely impairs on the strength of a concrete element. However, should the crack penetrate the full depth of the member water penetration problems may arise, or if the cracking is located in wet areas, future waterproofing techniques may be compromised. As such you should ensure you engage a building inspector who understands these concepts.
Case Study
During inspection of this property (photo at the top of the page) at practical completion we found that multiple plastic shrinkage cracks were evident throughout the slab. Upon consultation with our client we found that the slab was poured on a particularly hot day, and due to the slab depth being slightly increased, normal curing methods did not achieve the desired finish.